The Retorts.
It all began with an idea. To diversify the business & produce British Charcoal. In 2016 with the help of a Rural Development Grant from the Eastern Plateau Local Area Group funding body, we did just that and bought our first Pressvess Retort. Now, 7 years later, with demand for our charcoal exceeding all our expectations, we are upscaling the business by adding a second larger, more advanced Pressvess Retort. On this page you will find out all about the retorts and how they make Stag British Charcoal.
RTS1000 Prototype Single Barrel Retort
What is it?
The RTS1000 Prototype is a single barrel design retort, with a ‘charge drum’ and separate firebox. It was the FIRST Single Barrel Charcoal retort produced by Pressvess and its design and performance helped to develop future single barrel retorts.
It was designed to the budget available based on what we thought we might achieve when asking Lloyds Bank to help with match funding and achieving grant aid of 40%.
It is manufactured using 10mm thick high carbon ‘boiler plate’ steel, which is designed to withstand constant high temperatures & pressures.
The charge drum is 1m in diameter and 1.9m long.
It weights approximately 4.5 tonnes.
Depending on timber species, it can produce approximately 120 - 150kg of ungraded charcoal.
Since its manufacture in the Midlands and its delivery to our first base in Hertfordshire and the subsequent move to Cambridgeshire in 2023, it has produced in excess of 30 tonnes of charcoal!!
Designer & Manufacturer?
It was designed by the brilliant Nick Harris - a 5th generation charcoal maker and recognised as one of the best retort designers alive. Nick works in partnership with Roger Banister, Sarah Walker and the engineering team of wizards at Pressvess Turnkey Solutions who then manufacture some of the finest charcoal retorts in the world.
How does it Make Charcoal?
The RTS1000 is hand-loaded with seasoned timber in the format of firewood sized log and larger sections. The wood is thrown in to the back and stacked at the front, leaving a gap from the drum door of approximately 6 inches.
Once the ‘charge drum’ is filled with seasoned wood in the form of firewood type logs, a fire is lit in the separate firebox and the process of heating the wood can begin. The firebox is fed until the volatile wood / syn gases are released (Methanal amongst others). Then the top vent is closed which forces the gases back into the drum, where they self-ignite and a process called Pyrolosis which is the heating of wood without oxygen being present, this is how charcoal is produced.
A burn continues until all the ‘Syn’ gasses have been consumed. then the retort is left to cool for 24hrs and then once cool (below 40C), it can be unloaded, graded and bagged.
How Hot??
Just like lighting a fire, temperatures start low and then increase. Once all vents are closed and the process of Pyrolysis is underway, temperatures in the charge drum can reach 530C.
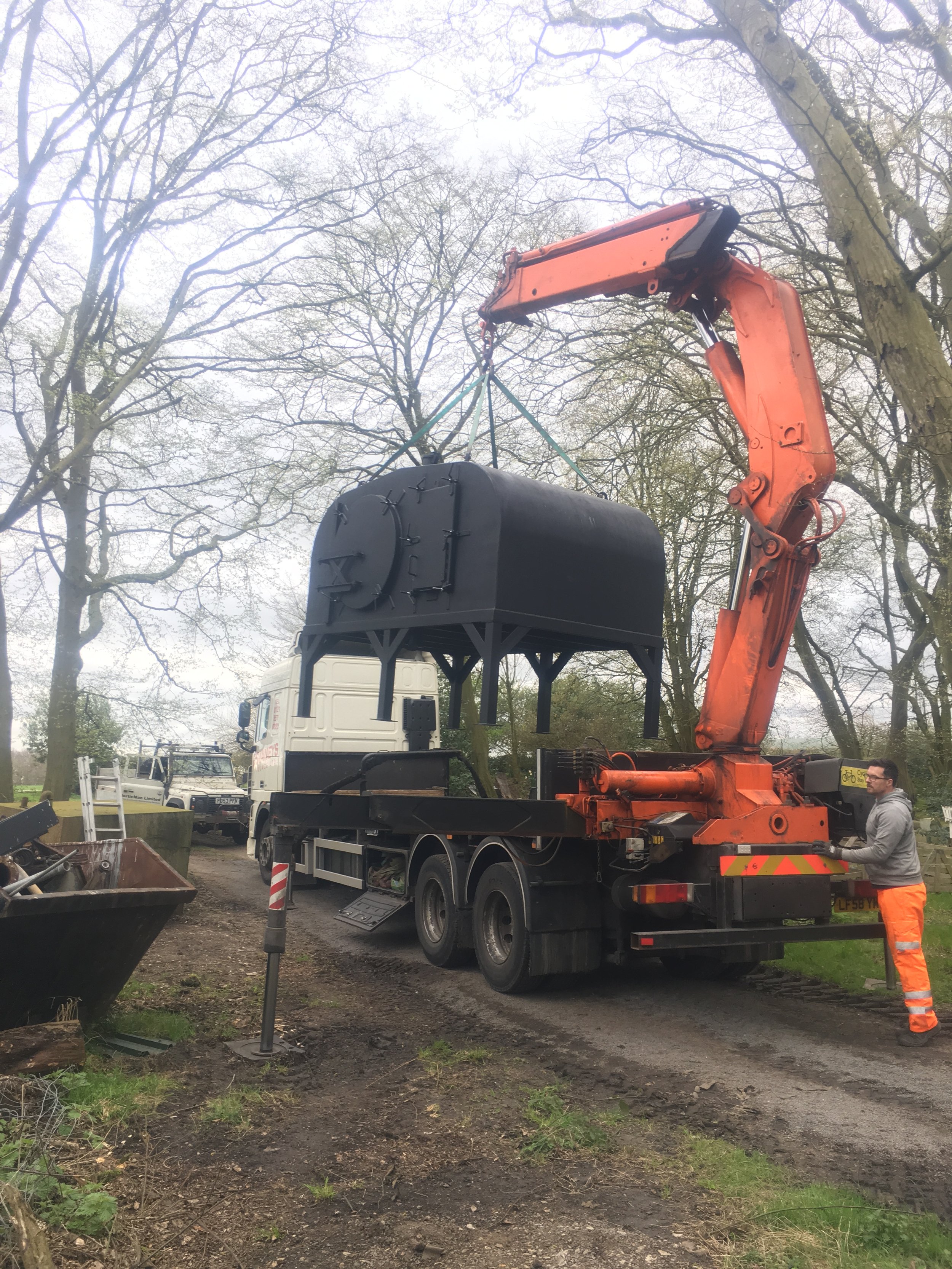
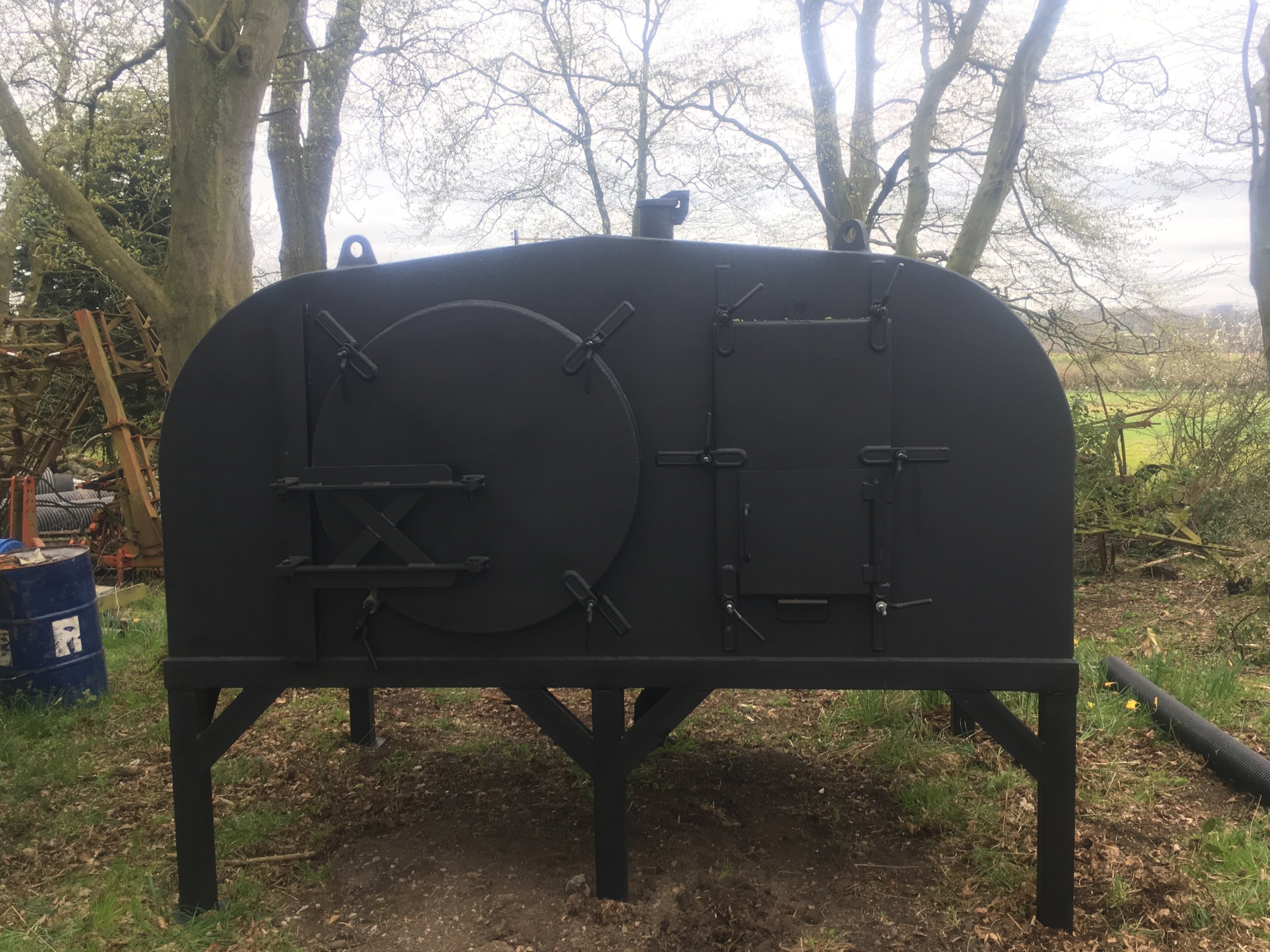
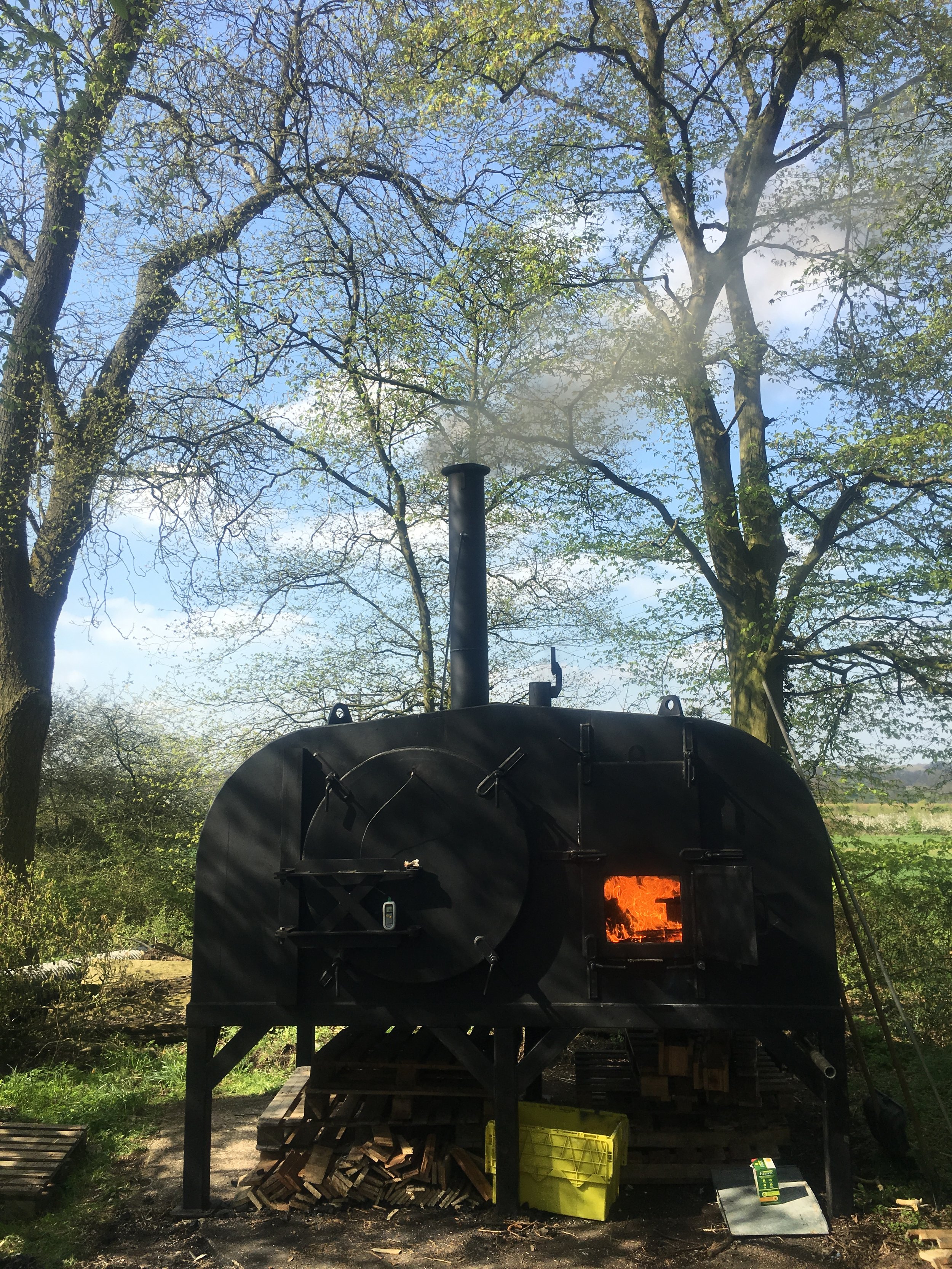
RTS1600 Single Barrel Retort with Cassettes
What is it?
The RTS1600 is the BIGGEST single barrel charcoal retort that Pressvess manufacture.
It is manufactured using 15mm thick high carbon ‘boiler plate’ steel, which is designed to withstand constant high temperatures & pressures.
The charge drum is 1.6m in diameter and 1.9m long.
It weights approximately 9.5 tonnes.
Designer & Manufacturer?
The RTS1600 has been designed yet again by the brilliant Nick Harris - recognised as one of the best retort designers alive. Nick worked in partnership with Roger Banister, Sarah Walker and the engineering team of wizards at Pressvess Turnkey Solutions to design & manufacture the RTS1600. It incorporates all the latest innovations that have been proven in previous retorts.
The retort was delivered in early November 2023, with commissioning by Nick Harris at the end of November.
What’s different about this one?
The RTS1600 is NOT hand loaded.
Processed and seasoned timber is tipped into special cassettes that are then inserted into the charge drum. The process of lighting the firebox and heating the wood is EXACTLY the same as it is with the smaller RTS1000, except we cook hotter - circa 550C but…… The big difference is that the cassettes allow us to unload the retort while it is much much hotter - circa 250 - 300C!
Cassettes are unloaded, place on a thick bed of sand, then covered with a close fitting airtight cover, which prevents the charcoal from igniting and allows the cooling down process to continue. In the meantime, a freshly loaded cassette can be inserted into the hot drum and as the retort is hot, allows for the next charcoal burn to be started the following day.
This then is the advantage of the Pressvess Cassette system, as it allows us to carry out a charcoal burn 3 - 5 times a week and thus meet the increased demand for our British Charcoal.
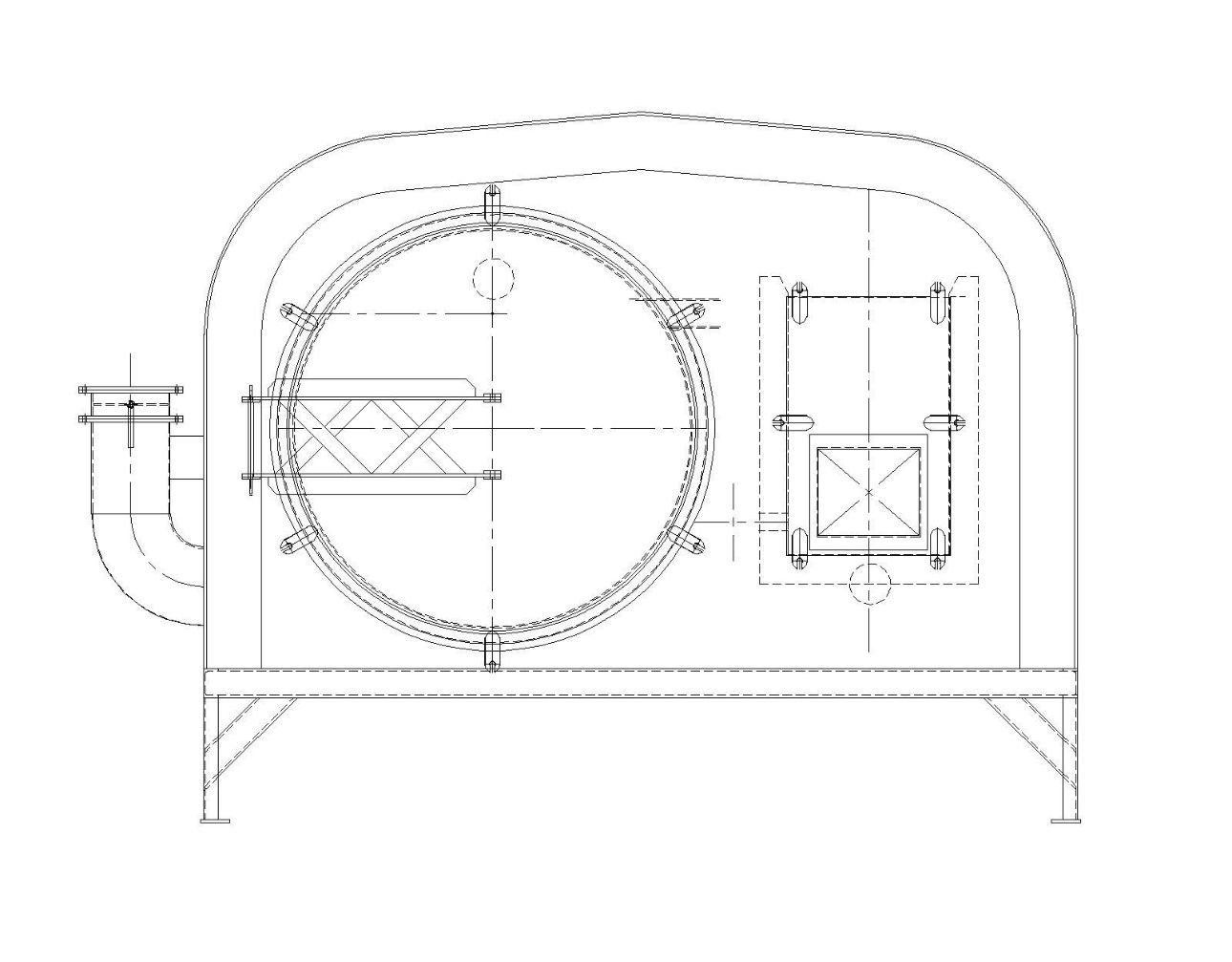
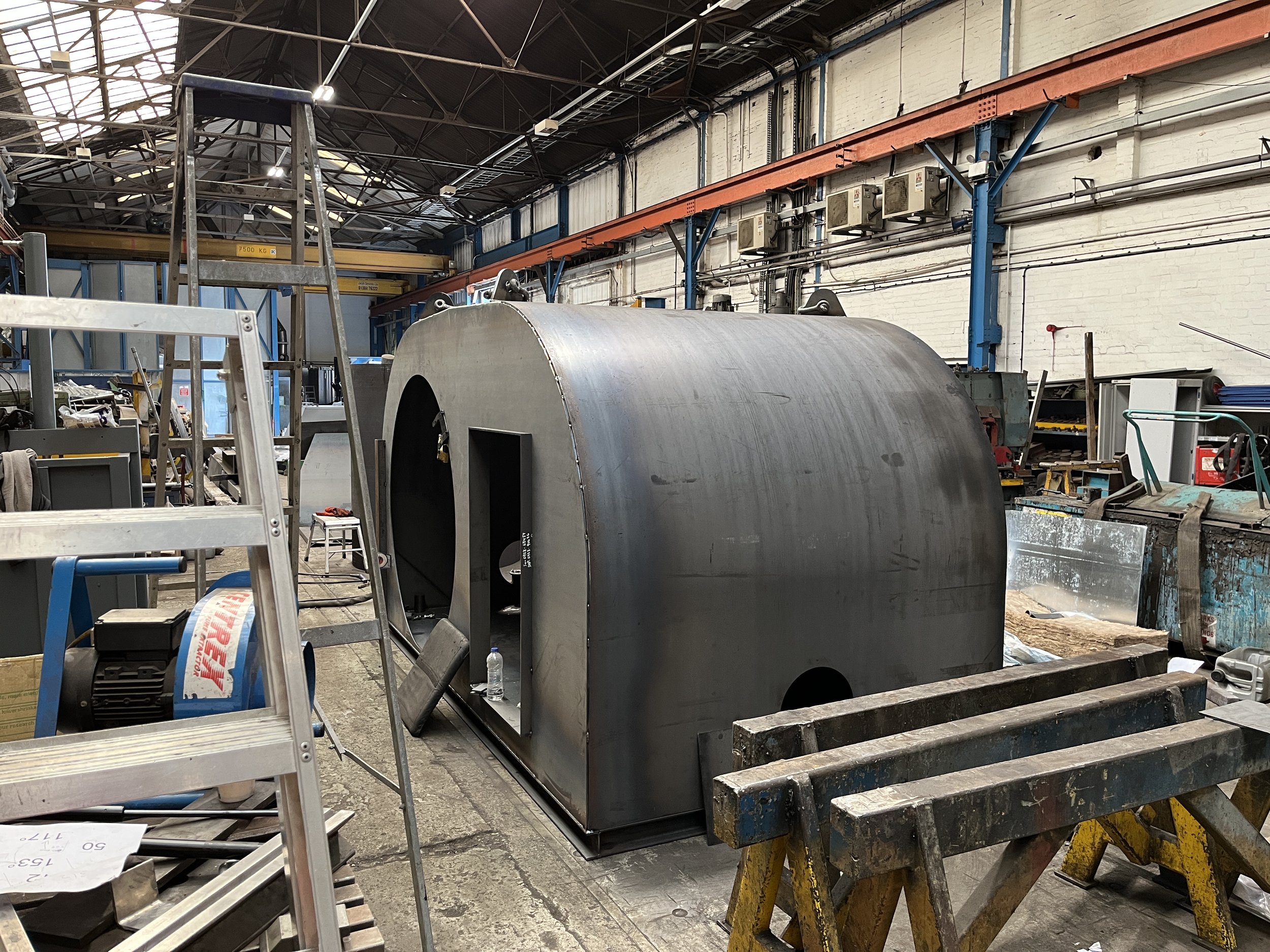
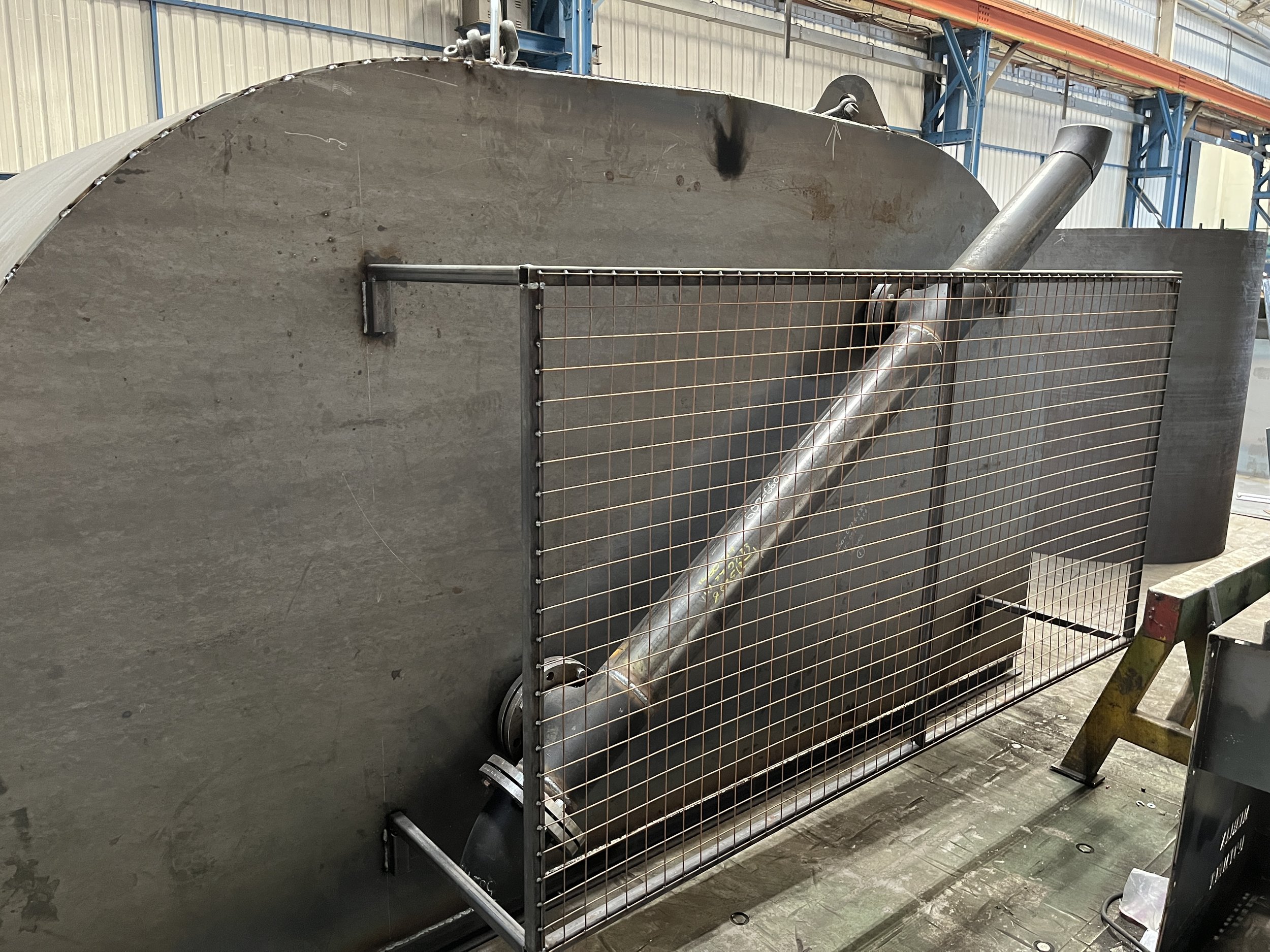
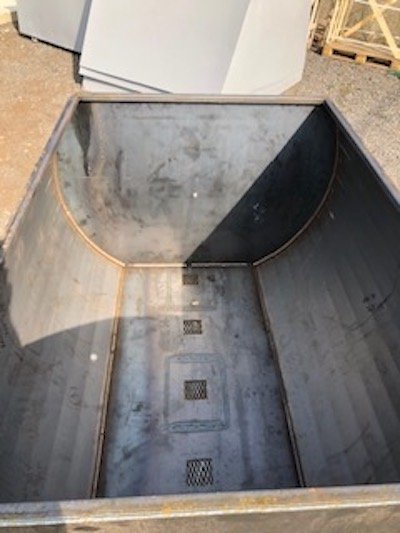
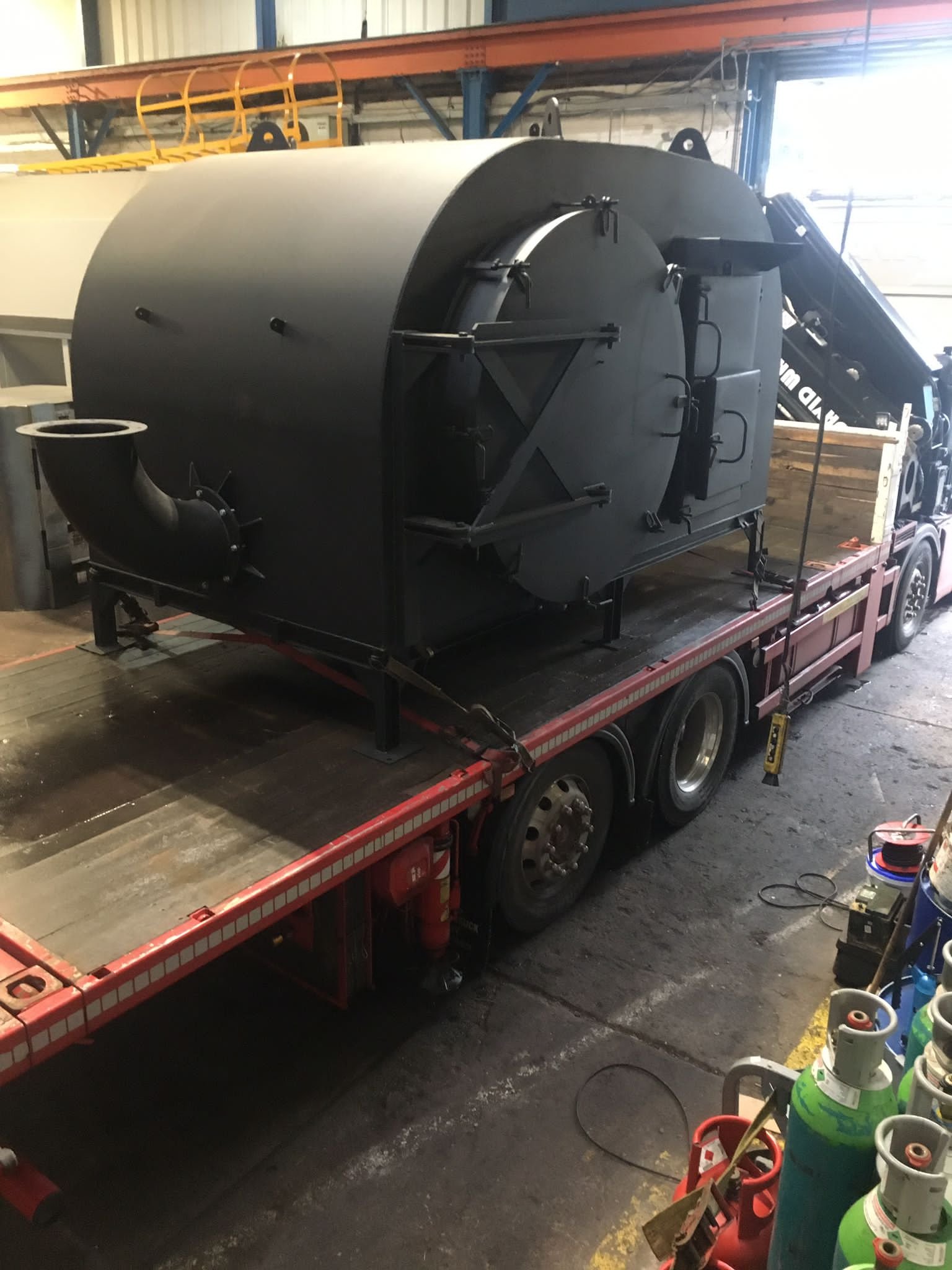
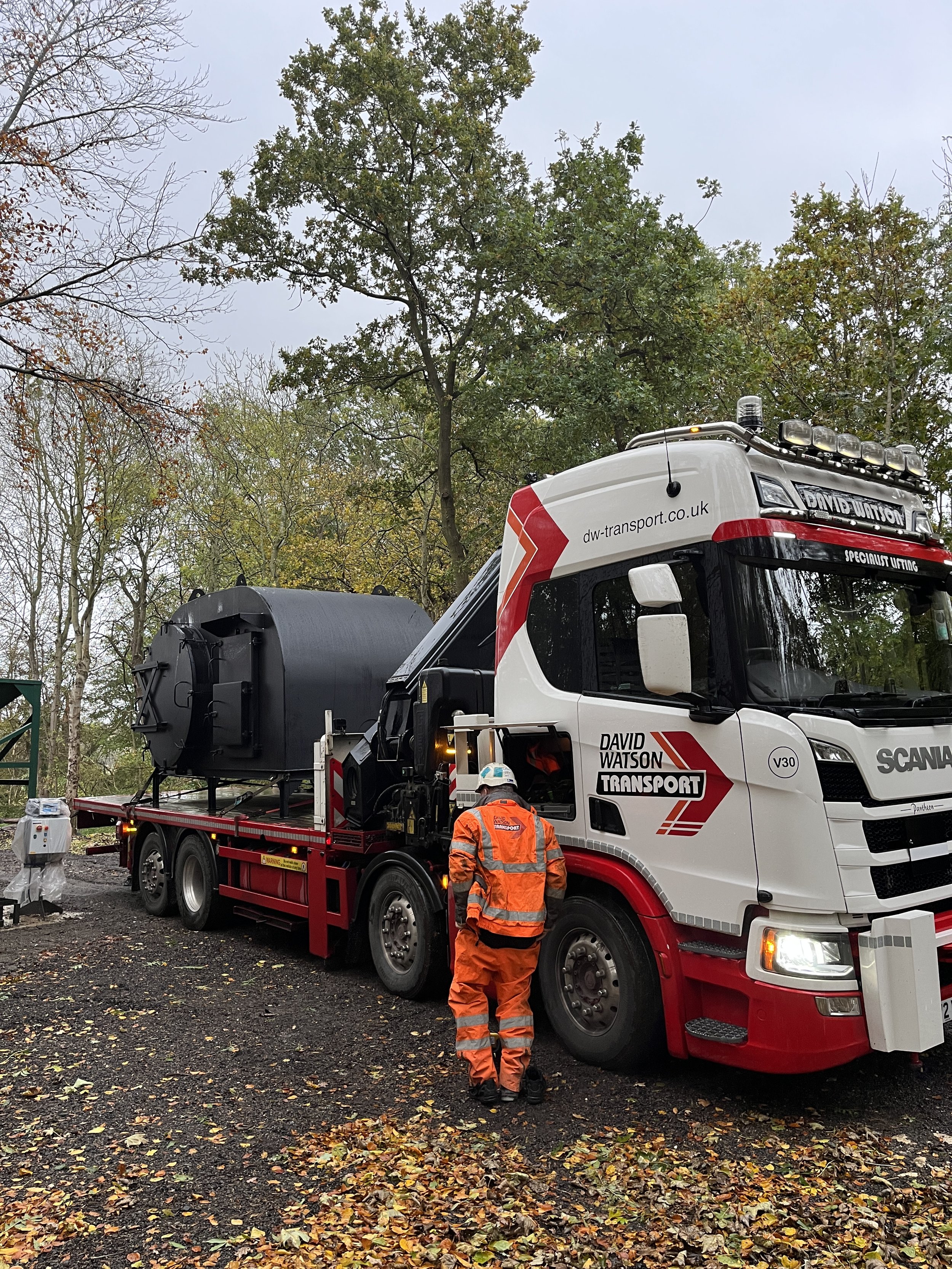
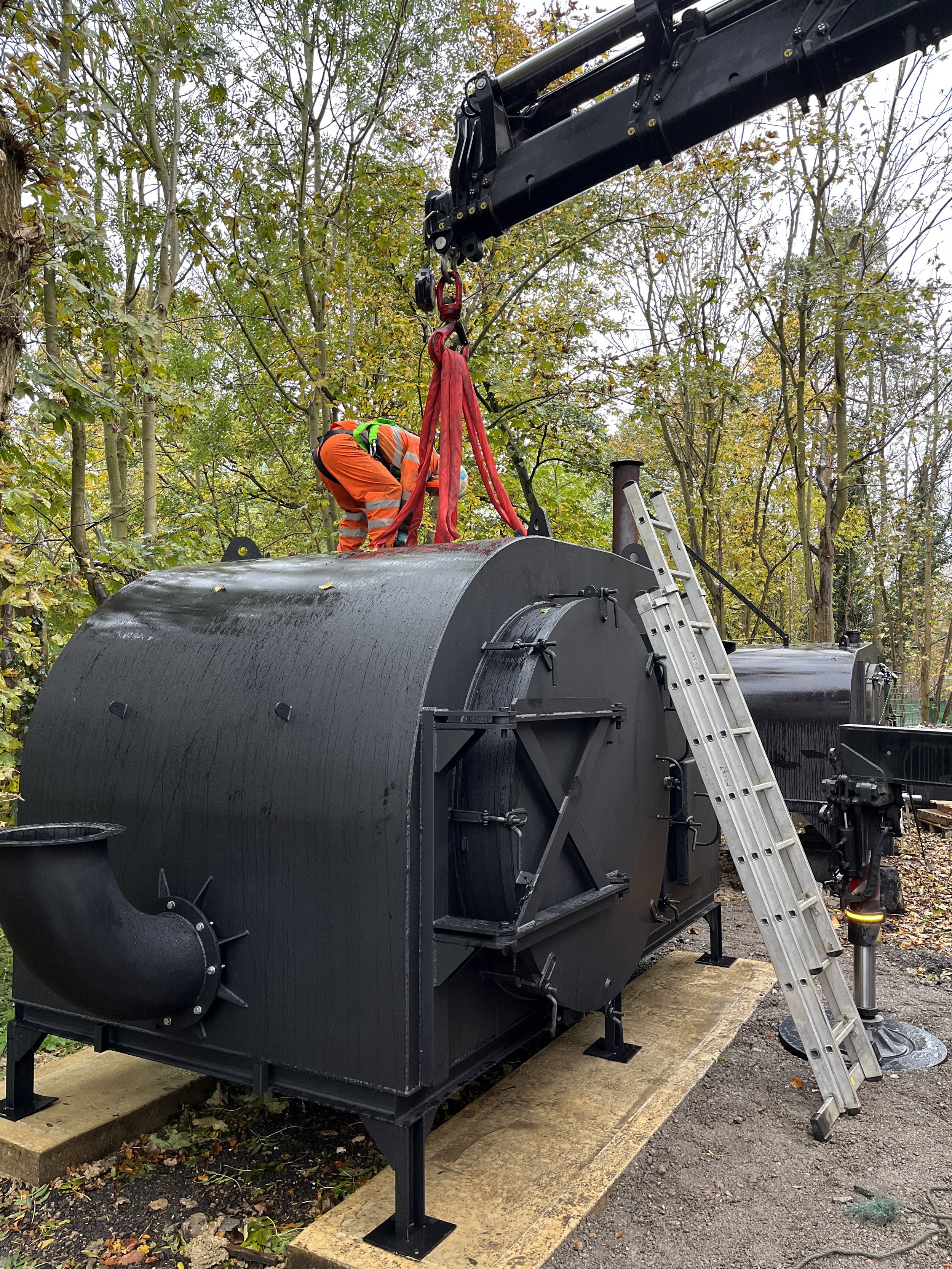
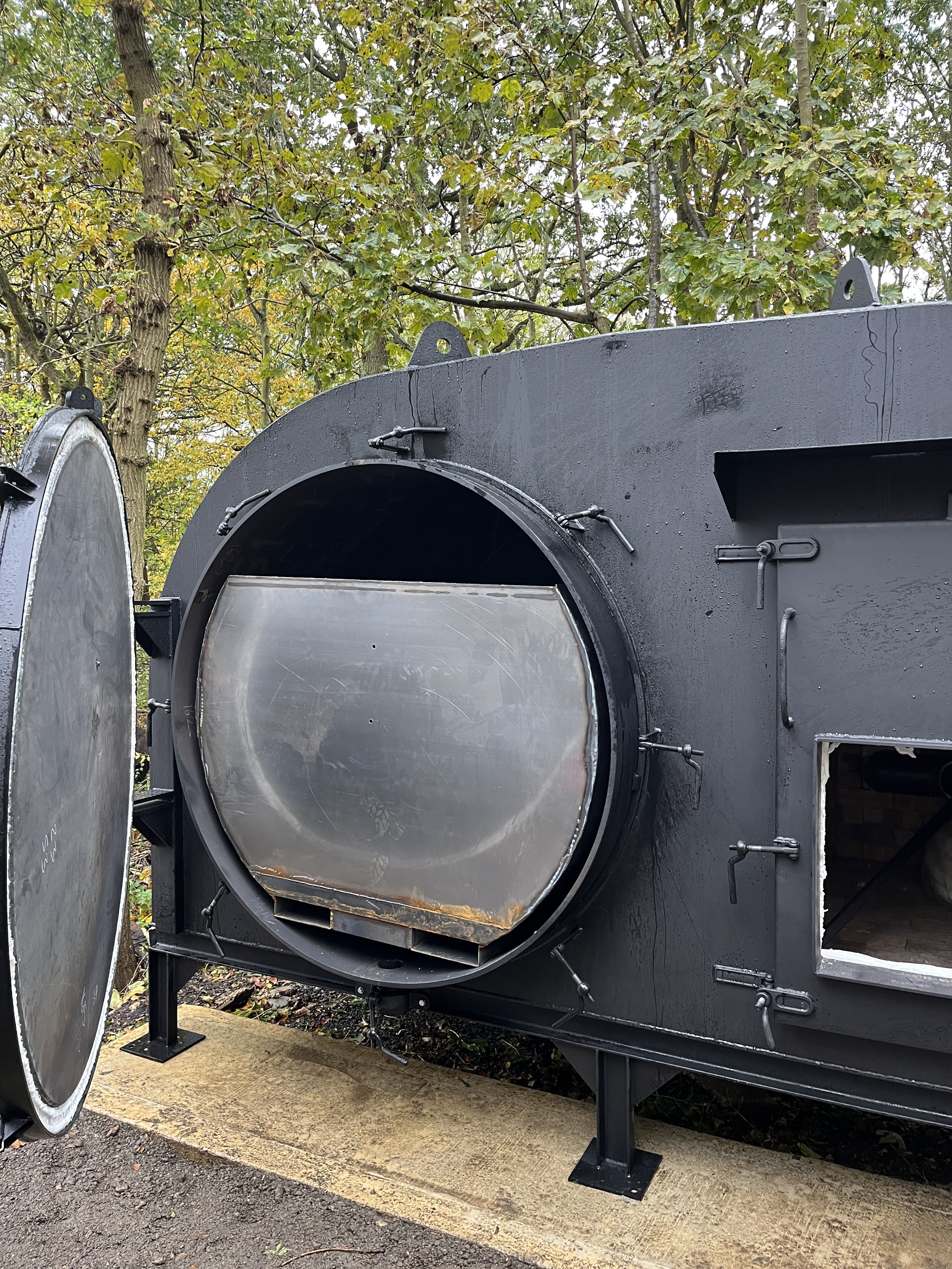
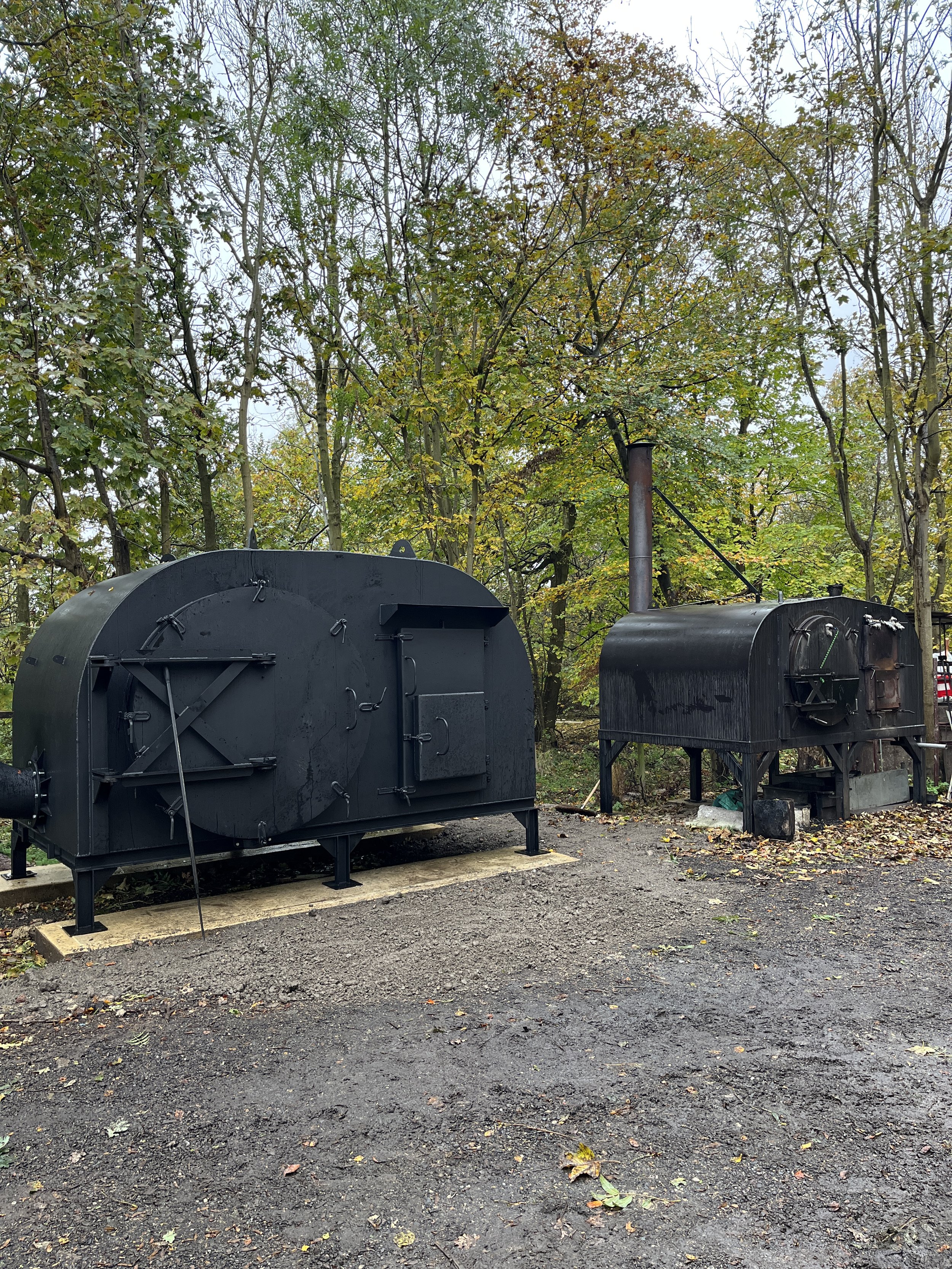
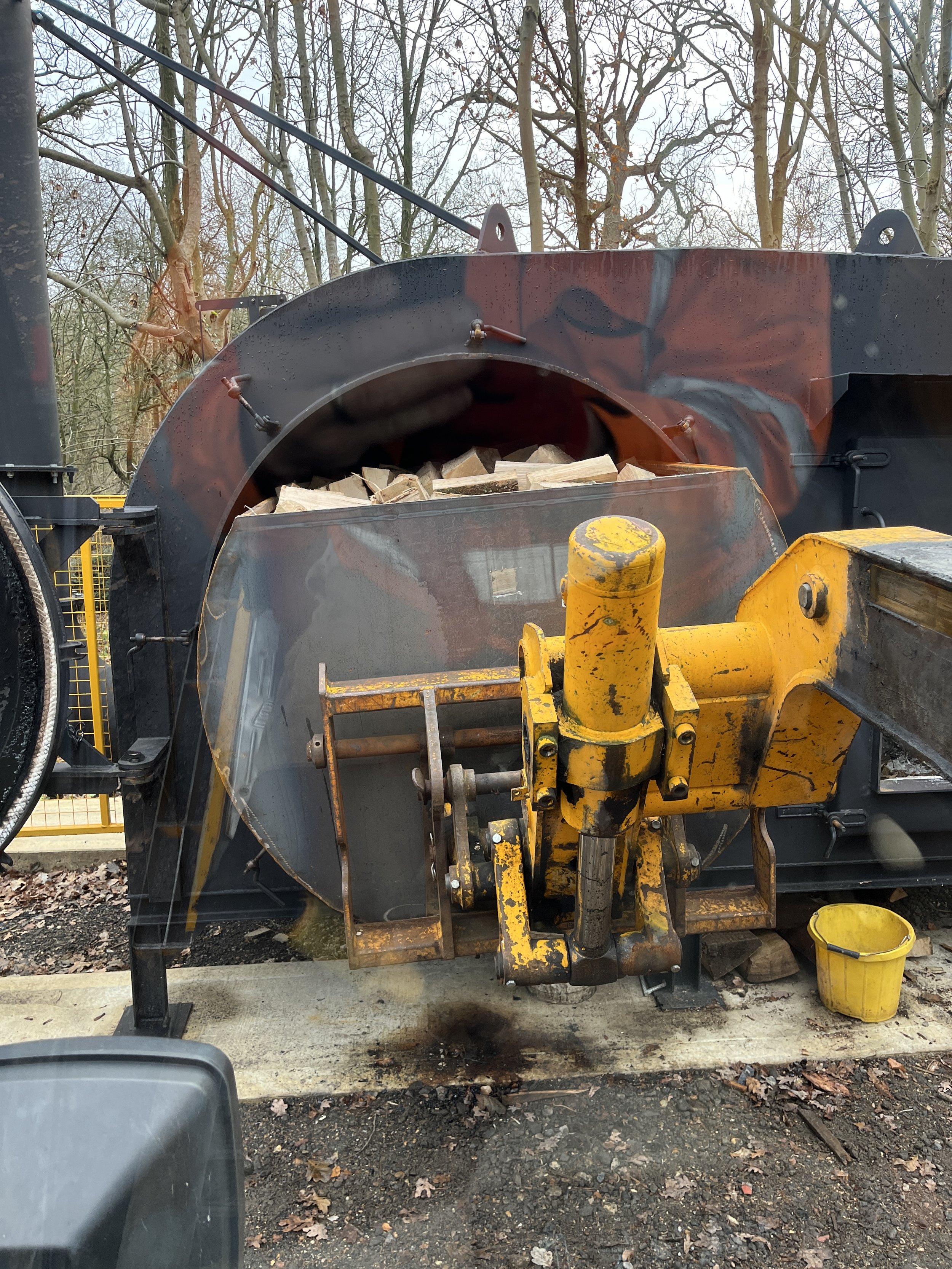
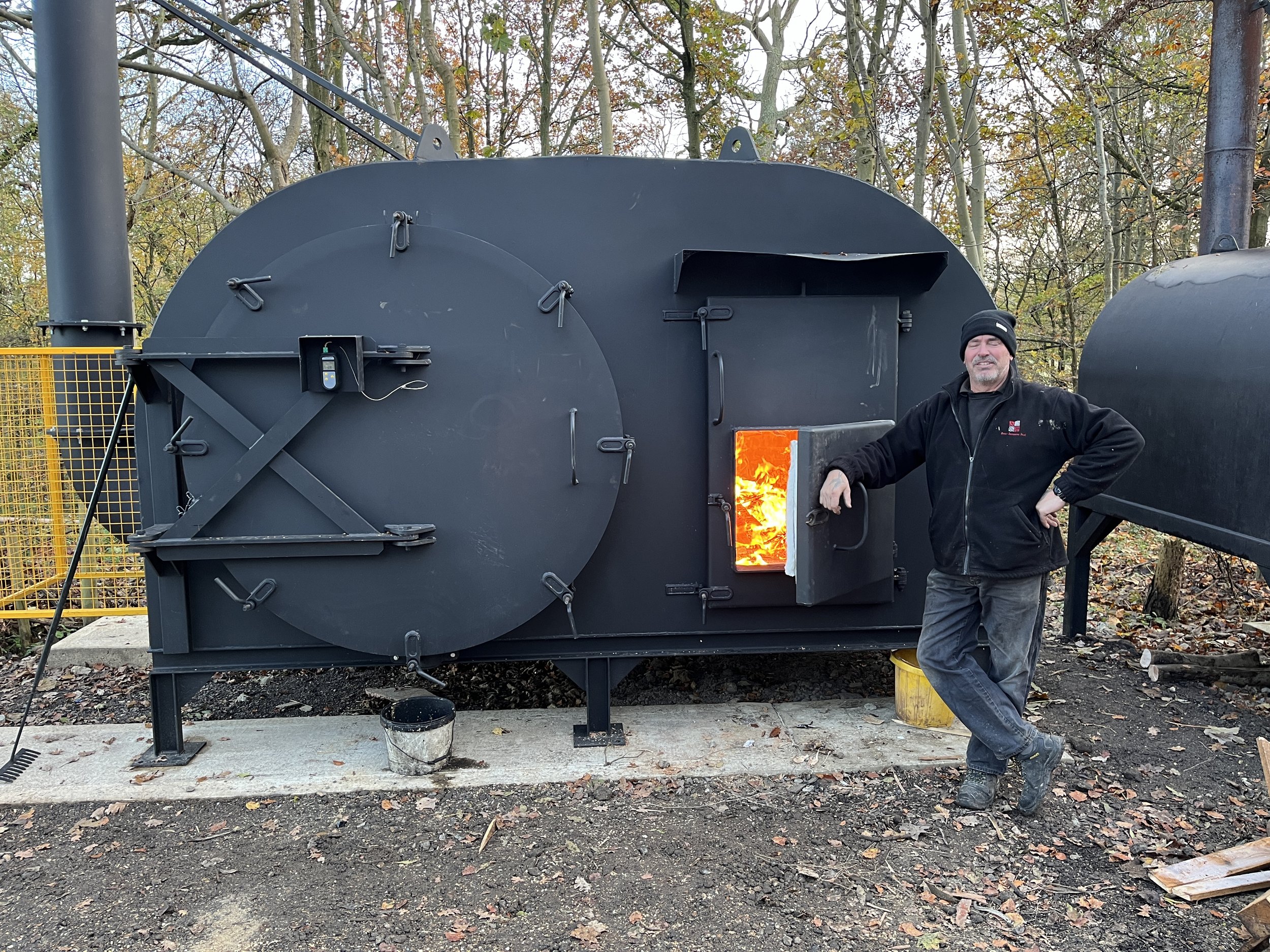
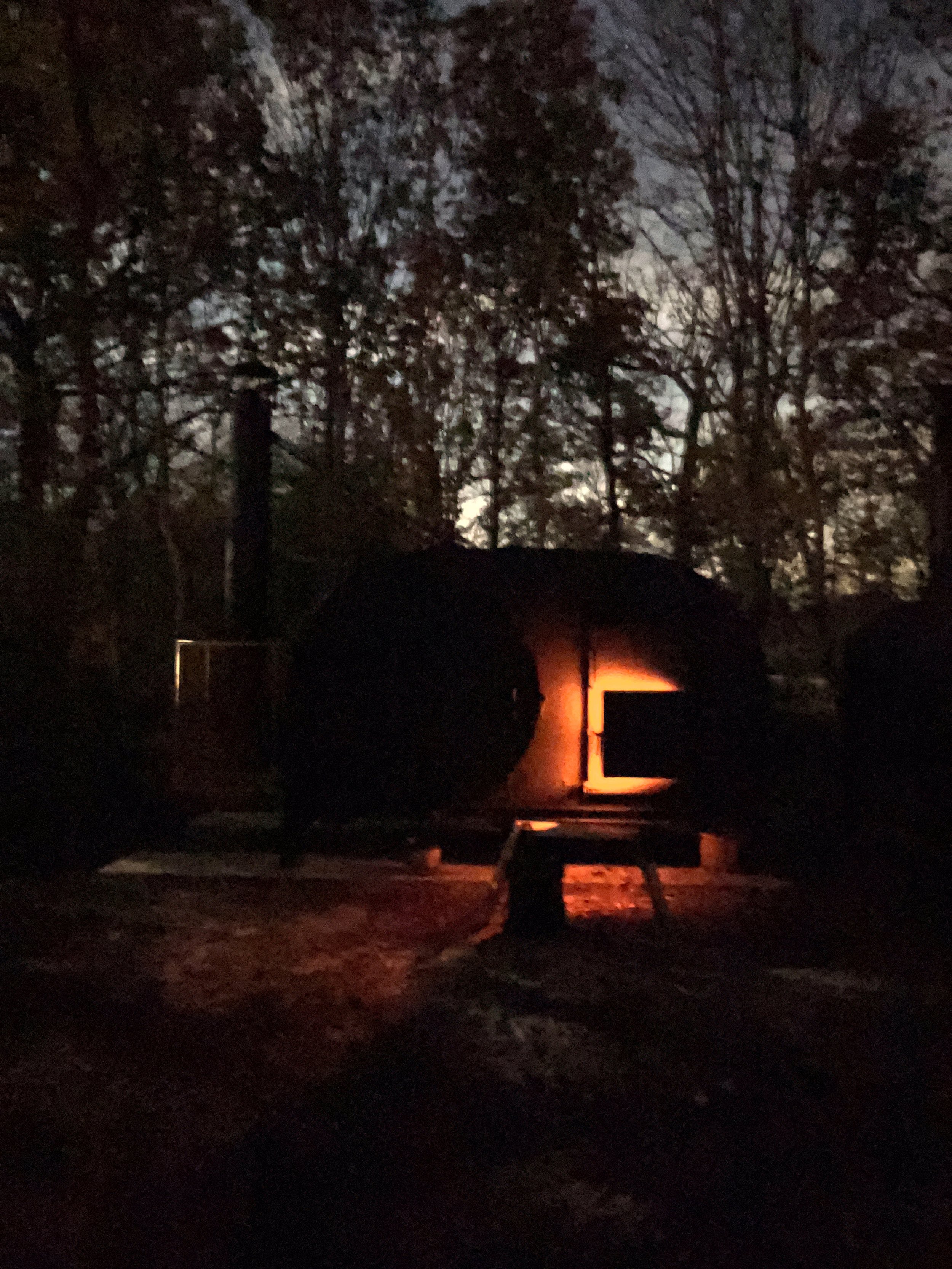
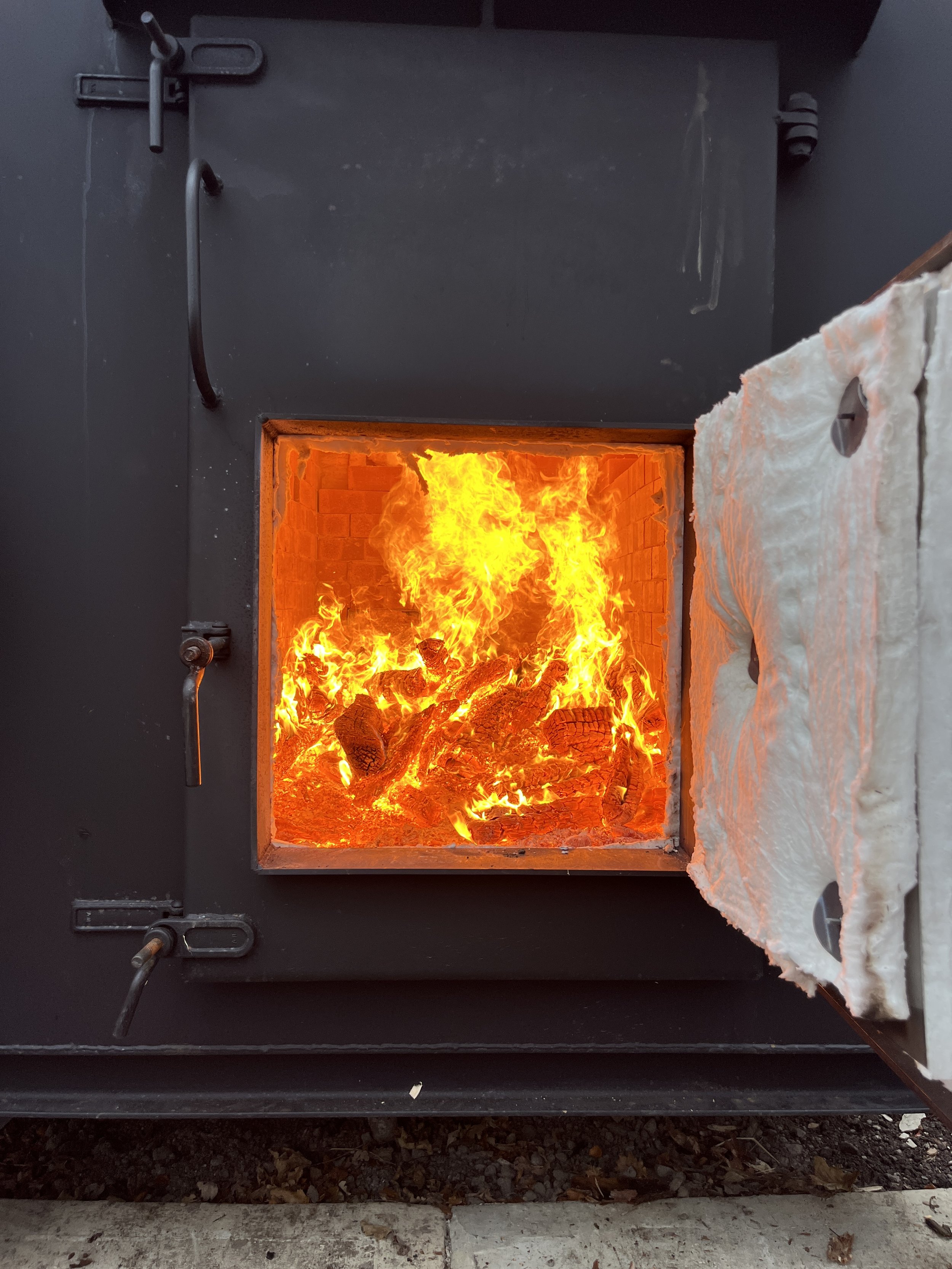
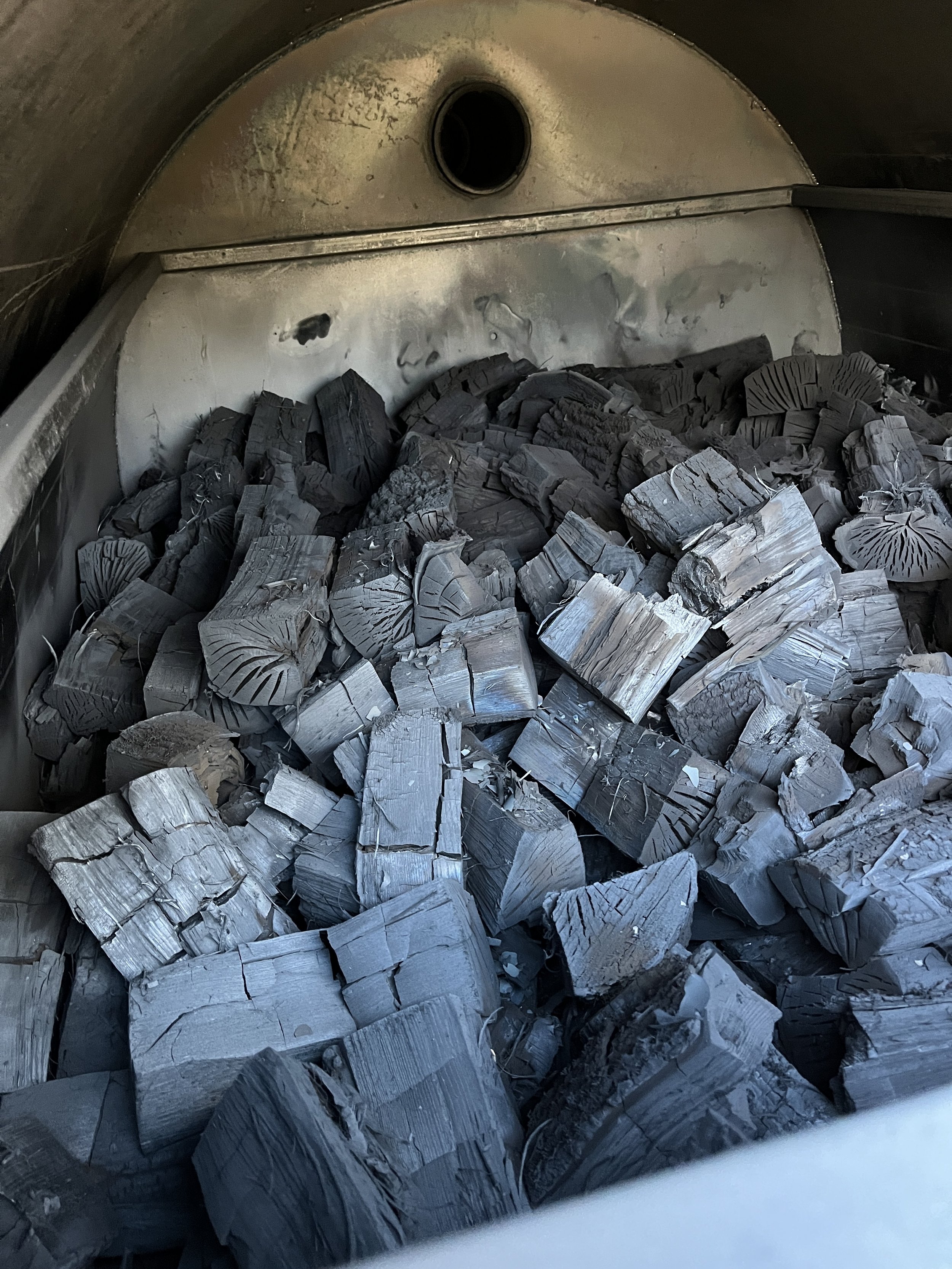
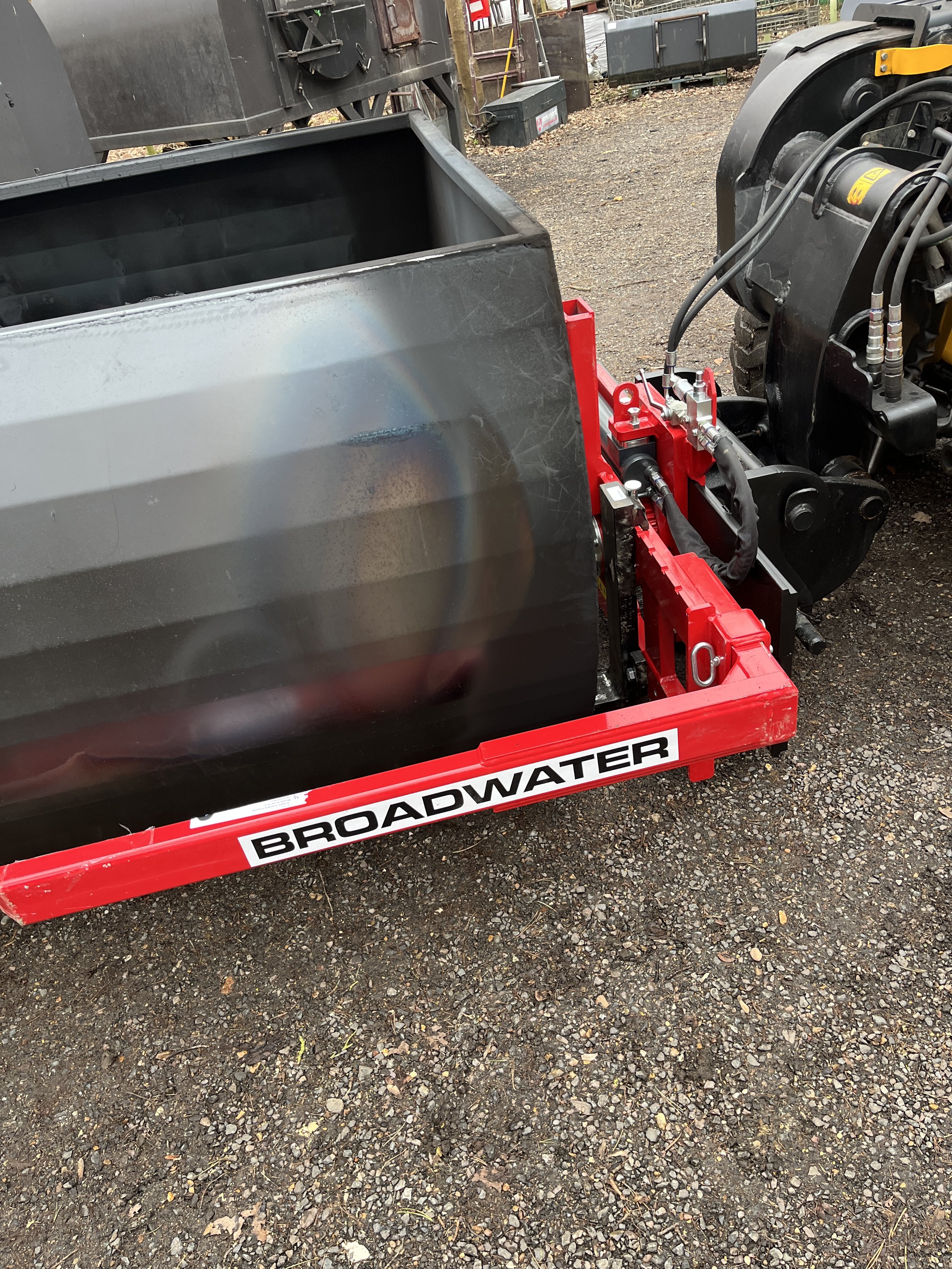